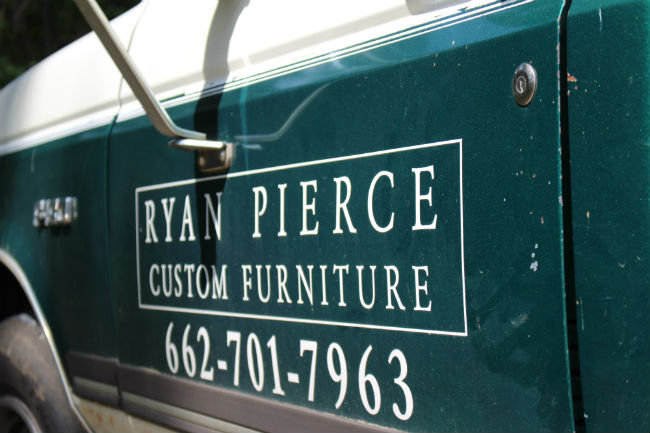
Ryan J. Pierce is a woodworker based just south of Oxford and north of Taylor. He works out of a wood shed in his backyard. He built the shed himself, though at the moment it doesn’t have any stairs and stands about two feet off the ground.
“It got off level and I needed to get under there, so I just pulled those out,” said Pierce. “I use to work under the house in the basement until I realized that I was going to need a lot more room so I built this space. It’s been good in some respects, because I’ve had to rely on hand tools.”

His hand tool approach has the added benefit of cutting down on much of the equipment he would otherwise need.
“Using hand tools, I make these shavings instead of saw dust,” said Pierce. “So I don’t need a large dust collection vent or a big drum sander, or any other large industrial pieces. It does take a little bit longer but I also think it adds a handmade feel to it. With that said I do plan on getting bigger tools at some point.”
Stepping into his workspace, the first item of note is a 10’ board laying across a worktable. The piece consists of 3 planks glued together that will act as a back to a commission he recently took on for a couple expecting a child.
“It’s going to be a toy box,” said Pierce, pointing to a chalkboard sketch of the project. “What I’m doing with this is leveling it out. This board is taller than the other two so you have to take your planer across.”

A Picasso quote is scrawled above the toy box design: “Action is the foundational key to success.”
Pierce’s first commissioned piece was a coffee table.
“I was talking to this guy at a party and ended up doing a table for him,” said Pierce. “I did a live-edge table, but when it was done he wouldn’t reply to texts or answer my calls.”
With a fully-built coffee table sitting around, Pierce decided to toss it up on Instagram and see if anyone else wanted it.
“You can still see it on my account, you just have to scroll way, way back,” said Pierce.
When Pierce started, he was making small figures as a hobby. Having just graduated from college he was looking for something to do other than go back for more school.
The bottom panel of the toy box rests against a wall. Two rows of three holes divide the piece into thirds. These holes are where the two wall panels will connect to the base. The majority of Pierce’s work typically does not utilize screws, and the pieces that do use them often hide the fact.

“I’ll use a screw if it’s the best thing,” said Pierce. “When you’re woodworking, you have to constantly be mindful of wood mobility. It’s a living material and as moisture comes in and out of a piece of wood it will expand and shrink. In quarries, they would take a wedge and drive it in a fissure. The wood would expand and crack open the rock. You can’t stop wood, it’s going to do what it wants to do.”
Great build quality is not just the goal, but for Pierce it’s the point of it all. When a commission leaves his workshop, he wants it to stand the test of time.
“I try, as much as I can, to be in the business of making furniture that will last generations so their grandkids can have it as an heirloom,” said Pierce.
That goal starts with having high quality wood to use for each project, which is what led him to open Oxford Slab and Lumber Co. with John Haltom.
“There’s not really any one place to get it around here, you just have to find it where you can,” said Pierce. “Which is part of why we opened the saw mill.”

Owning their own mill allows them to not only have a direct supply, but to also oversee processing of the wood every step of the way.
“You have to get the moisture content of the wood down before you can actually use it,” said Pierce. “You’ll start with a slab and let it air dry through what’s called stack and stickering. You’ve got to stack it in a specific way so that air can move through it and then you let it sit for a year or two.”
By then the wood should be down to 12% moisture content, but that number still needs to be brought down.

“Houses with central air are about 6%, back in the day they’d just use the air dried wood because they didn’t have central air constantly pulling moisture out,” said Pierce.
To reach the final step of processing the lumber, you’ll need a wood kiln. Types of kilns vary from solar-heated to massive industrial-grade machines. Pierce and Haltom are currently towards the end of building their own kiln for Oxford Slab and Lumber Co.
“This one just catches the sun,” said Pierce. “We’ve got the walls painted black to help absorb heat and we’re putting this clear roofing on top to let the sun in and magnify it. ”
Hearing the amount of knowledge Pierce has regarding woodworking and seeing what he is capable of building, you’d be surprised to find out how humble he has remained. Despite having an impressive portfolio, the Oxford woodworker is only looking forward.
“I’ve been doing this for 6 years and, you know, I wish I had even more experience,” said Pierce. “I’m getting there and I still have a lot to learn, but I know a lot more than I did before.”